alumina hydrate
originally presented at the Green Task Force booth, NCECA 2021
Rio Tinto Alcan
The alumina hydrate that we receive at the University of Montana is distributed through Rio Tinto Alcan (RTA), a mining and distribution parent company that mines many raw materials through several companies all over the world. Bauxite, through RTA, is mined in Porto Trombetas, Brazil, Weipa, and Gove, Australia. The raw bauxite then travels to their respective refineries in Alumar, Brazil, Yarwun, and Queensland, Australia. Their home office is in Montreal, Quebec, Canada.
Mining and Refining Bauxite for Alumina
The process of refining bauxite into alumina is a lengthy one, and one that requires quite a lot of waste and resource consumption. It begins with the Bayer process, developed by Carl Josef Bayer in 1888. The alumina compounds are amphoteric, meaning they are both acidic and basic, so when heated to 302 to 392 degrees Fahrenheit in a pressure vessel with a caustic soda solution, the alumina is dissolved and leaves solids behind for βred mud,β or impurity extraction. This mixture is then filtered and seeded with aluminum hydroxide crystals from previous extractions to encourage solid alumina crystal growth. Solid impurities are then filtered out and discarded, often by using a rotary sand trap and a flocculant. The waste, often containing iron oxides, silica, calcium, and titanium, is removed, and alumina remains. 1.9 to 3.6 tons of bauxite, depending on the amount of impurities, is required to produce one ton of alumina oxide. Much of the aluminum ore in the process is dissolved, creating waste. The energy used is most often thermal, and between 7 GJ to 21 GJ is expended (One gigajoule (GJ) is equal to 1 billion joules. One gigajoule is equal to 277.8 kilowatt hours (kwh). For reference, 200kwh is enough to power a small home for a month.). For consumption outside of the ceramics field, this material is then used in the Hall-Heroult process to create aluminum.

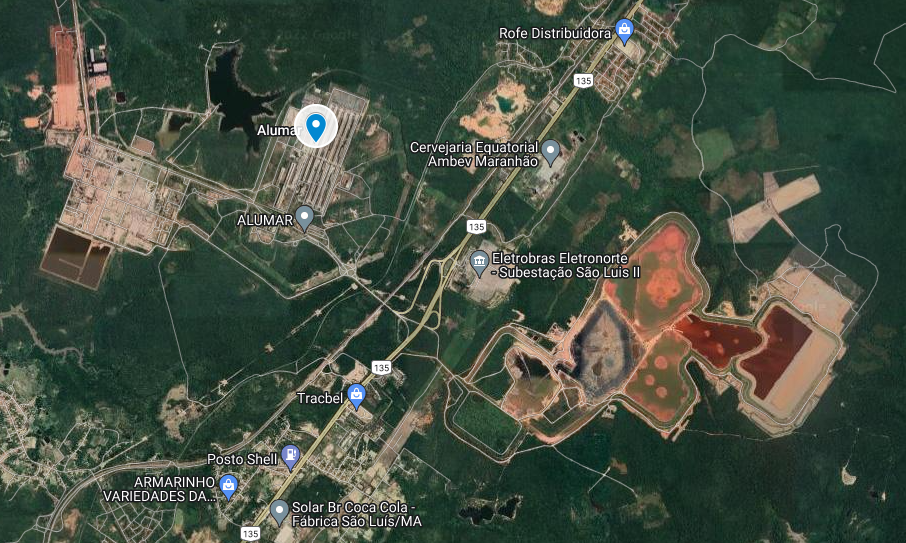

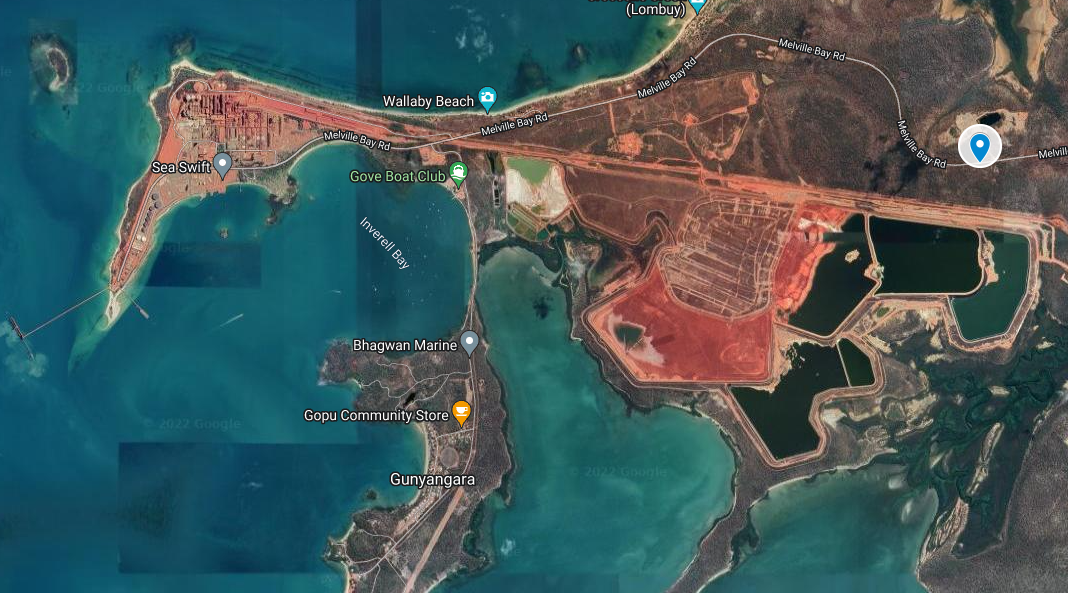


Alumina hydrate is a source of aluminum that is often smelted and used to create bicycles, automotive and architectural materials, and more, so the effect on the environment is tied to industry and general consumerism.
Routes
Between Porto Trombetas and Alumar, Brazil, the raw material travels 1,451 nautical miles. After being refined in Alumar, the product is then shipped 3,991 miles to Montreal for distribution, 2,900 miles to Laguna, California, 1,025 miles to Helena, Montana, and finally 113 miles to Missoula, Montana, where it arrives at UM for use by ceramics students. This material alone travels approximately 9,700 miles over the course of its manufacture and distribution.
To see each location and their possible routes, click here.